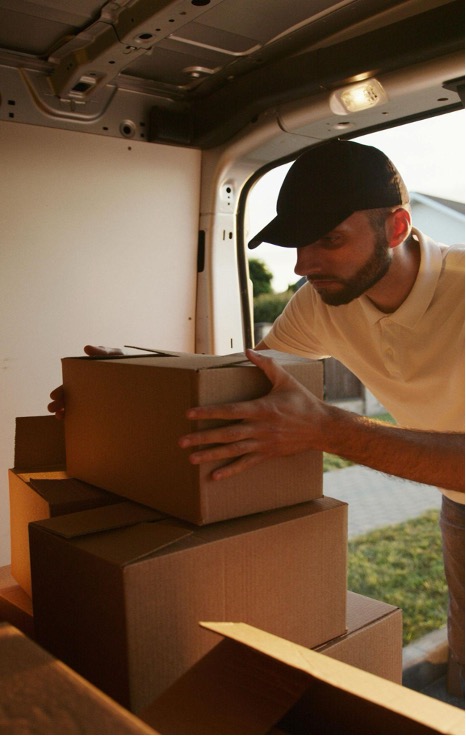
What Goes Into the Cost of Fulfillment?
Fulfillment is a crucial part of any eCommerce business. It’s the process of receiving, storing, packaging, and shipping products to customers. However, many businesses overlook how fulfillment costs can add up. Understanding these costs and optimizing them can significantly improve profitability. In this guide, we'll break down the various factors that contribute to fulfillment costs and offer strategies to help you reduce them.
Key Components of Fulfillment Cost
Fulfillment costs aren't just about shipping fees. Several elements make up the total cost of getting your product to the customer, and each of them plays a crucial role in determining your bottom line. Let's take a deeper look at the primary components.
Warehousing and Storage Costs
Storage is one of the primary contributors to fulfillment costs, particularly if you’re working with inventory on a large scale. Here are the key factors that influence warehousing and storage expenses:
- Space Rental or Ownership: Renting warehouse space or owning your own facility both incur costs, depending on the size, location, and scale of operations. Leasing is the most common option for many eCommerce businesses.
- Inventory Management Systems: Efficiently managing stock comes at a cost. Warehouse management software (WMS) helps keep track of inventory levels, but it can also be expensive.
- Utility and Maintenance Expenses: The costs of utilities such as electricity and water, along with regular warehouse maintenance, contribute to overall fulfillment costs.
Packaging and Materials
Packaging materials are an essential part of your fulfillment process, but they can also significantly impact costs. Here's what to consider:
- Standard Packaging: The cost of boxes, packing materials, and protective elements like bubble wrap or foam can vary based on the size and fragility of your products. If you ship large or delicate items, packaging costs can add up quickly.
- Custom Packaging: While custom packaging can make your product more appealing to customers, it often comes with a higher price tag. However, it can also help build brand recognition and reduce damage during shipping.
Labor Costs
Labor is another significant cost in fulfillment. From warehouse staff to fulfillment center workers, wages can fluctuate depending on the type of work being done and the time of year. Here's how labor costs factor into fulfillment:
- Warehouse Staff and Fulfillment Personnel: Employees who handle receiving, storing, packing, and shipping products are key to the fulfillment process. Their wages add to your fulfillment cost.
- Seasonal Labor Variations: Many businesses experience spikes in fulfillment during the holidays or peak seasons, meaning they may need to hire temporary or seasonal staff, which increases costs.
- Outsourcing vs. In-house Labor: Some businesses may choose to outsource fulfillment to third-party logistics (3PL) providers, while others may choose to handle it in-house. Outsourcing can provide economies of scale and reduce labor costs, but it can come with additional service fees.
Shipping and Transportation Expenses
Shipping is often the largest single component of fulfillment costs, and understanding how shipping works can help you manage and reduce these expenses.
- Shipping Carriers and Rates: The choice of carrier (e.g., FedEx, UPS, USPS) will affect the cost of fulfillment. Each carrier has its own pricing structure based on weight, size, and destination.
- Impact of Order Volume and Weight: The larger the order or the heavier the package, the more expensive it is to ship. Shipping costs also increase with volume—more orders typically lead to more spending.
- Shipping Zones and Distance: Shipping to farther zones increases costs because of the longer distance. This is especially relevant if you're shipping internationally, where costs can rise significantly due to customs and longer shipping routes.
Technology and Automation Costs
Investing in the right technology can streamline fulfillment and save money in the long run. Here's how:
- Fulfillment Software and Management Systems: Fulfillment software helps automate order processing, inventory tracking, and shipping label creation. While this software requires an initial investment, it can help you cut costs by improving accuracy and efficiency.
- Automation Tools: Conveyor belts, robots, and sorting machines can help speed up the fulfillment process. While these tools require significant upfront investment, they can reduce the need for manual labor and cut costs over time.
- How Technology Reduces Long-Term Costs: By investing in technology, you can reduce human error, increase speed, and scale operations without dramatically increasing costs.
Order Accuracy and Error Handling
Order accuracy is critical in fulfillment, as errors can lead to costly returns, customer dissatisfaction, and inventory imbalances.
- Cost of Errors in Fulfillment: Mistakes such as mis-shipments, damaged goods, or incorrect inventory updates can cost your business money. Handling returns, correcting mistakes, and re-shipping orders all add to fulfillment costs.
- Quality Control Measures: Implementing quality control measures, like barcode scanning, can help reduce errors and improve accuracy, which ultimately lowers the cost of handling mistakes.
- Efficient Order Processing: Streamlining order fulfillment processes and implementing a robust checking system can reduce human error, saving time and money in the long term.
Returns Processing
Returns are an inevitable part of eCommerce, but they come with additional costs. Here's what goes into returns processing:
- Restocking Fees: Some businesses charge a restocking fee to cover the cost of inspecting and updating returned inventory.
- Repackaging: Returned items often need to be repackaged, especially if the original packaging was damaged during the return process.
- Inventory Updates: After processing returns, inventory systems need to be updated, which can incur additional labor and system costs.
- Reducing Return Rates: Better order management and improved product descriptions can help reduce returns, which in turn helps reduce fulfillment costs.
Optimizing Fulfillment Costs
Understanding fulfillment costs is only part of the equation—optimizing them can make a huge difference to your business’s profitability. Here are some strategies to help reduce these costs:
- Partnering with 3PL Providers: Outsourcing to third-party logistics providers (3PLs) can help streamline your fulfillment process. A 3PL often has the infrastructure and expertise to lower fulfillment costs.
- Improving Efficiency: Strategies like zone skipping (shipping products directly to fulfillment centers closer to customers) and batch processing (grouping similar orders together for more efficient picking and packing) can reduce labor and shipping costs.
- Bulk Shipping Discounts: Many carriers offer discounts for bulk shipping. If you can consolidate shipments, you may be able to secure better rates.
Conclusion
Fulfillment costs are complex and encompass several key components, including warehousing, packaging, labor, shipping, and technology. By understanding these factors and implementing strategies to optimize them, you can reduce your fulfillment costs and improve profitability.
If you’re looking to take your fulfillment process to the next level, Slotted can help.