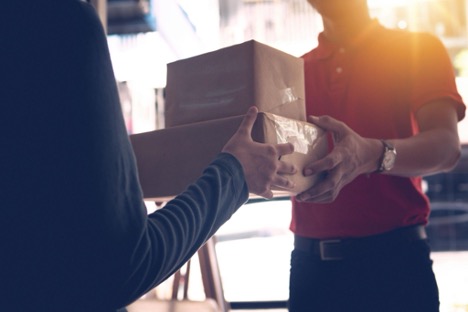
How to Find the Right Pick and Pack Warehouse
Finding the right pick and pack warehouse is crucial for businesses looking to streamline their order fulfillment processes and enhance customer satisfaction. A pick and pack warehouse specializes in handling orders by picking items from inventory, packing them, and preparing them for shipment.
Choosing the right partner can significantly impact your business's efficiency and success. In this guide, we'll walk you through how to find the ideal pick and pack warehouse to meet your specific needs.
Understand Your Business Needs
Before you start searching for a pick and pack warehouse, it’s important to understand your own business requirements. This involves assessing your order volume, product types, and fulfillment goals.
Assess Order Volume and Product Types
Evaluate your average order volume and the types of products you handle. Are your orders large and complex, or are they small and simple? Understanding these factors will help you find a warehouse that can efficiently handle your specific requirements.
Consider Your Shipping Regions and Customer Base
Identify where your customers are located and where you need to ship products. A warehouse’s location can impact shipping times and costs, so choose a warehouse that aligns with your geographic distribution needs.
Define Your Fulfillment Goals
Determine what you want to achieve with your fulfillment operations. Are you focused on speed, accuracy, scalability, or a combination of these factors? Clearly defining your goals will help you select a warehouse that aligns with your objectives.
Key Factors to Consider When Choosing a Pick and Pack Warehouse
When evaluating potential pick and pack warehouses, there are several key factors to consider:
Location
Proximity to Suppliers and Customers: The location of the warehouse can affect shipping times and costs. Ideally, it should be strategically located to minimize delays and reduce shipping expenses.
Impact on Shipping Times and Costs: A well-positioned warehouse can help you meet delivery deadlines and keep shipping costs manageable. Consider the warehouse’s proximity to major transportation hubs and your customer base.
Scalability
Ability to Grow with Your Business: Choose a warehouse that can accommodate your growth. It should have the capacity to handle increased order volumes as your business expands.
Handling Seasonal or Unexpected Volume Spikes: Ensure the warehouse can manage fluctuations in order volume, whether due to seasonal trends or sudden surges in demand.
Technology and Integration
Warehouse Management Systems (WMS): A modern WMS is essential for efficient inventory management and order processing. Check if the warehouse uses advanced technology to track inventory and manage orders.
Integration with Your E-commerce or Inventory Systems: Ensure the warehouse can integrate with your existing systems for seamless data flow and real-time updates.
Efficiency and Accuracy
Track Record for Order Accuracy and Timeliness: Look for a warehouse with a proven track record of accurate and timely order fulfillment. Ask for performance metrics and case studies if available.
Use of Automation and Technology: Evaluate the warehouse’s use of automation and technology to streamline processes and reduce errors. Automated systems can improve efficiency and accuracy.
Cost Structure
Transparency in Pricing: Seek a warehouse with a clear and transparent pricing structure. Avoid warehouses that have hidden fees or unclear cost terms.
Understanding Cost-per-Order vs. Bulk Order Fulfillment Pricing: Understand the warehouse’s pricing model. Some warehouses charge per order, while others may offer bulk order pricing. Choose a model that aligns with your business needs.
Services to Look for in a Pick and Pack Warehouse
In addition to the core pick and pack services, consider the following value-added services:
Value-Added Services
Kitting, Labeling, and Returns Management: Look for warehouses that offer additional services such as kitting (assembling products), shipping labels, and managing returns. These services can enhance your fulfillment process.
Inventory Tracking and Real-Time Reporting: Ensure the warehouse provides comprehensive inventory tracking and real-time visibility & reporting to keep you informed about your stock levels and order status.
Custom Packaging and Branding Options: If branding is important to you, find a warehouse that offers custom packaging options to enhance your brand’s visibility.
Vetting and Comparing Warehouses
Once you’ve narrowed down your options, it’s time to vet and compare potential warehouses:
Requesting Quotes and Conducting Site Visits
Request Quotes: Obtain detailed quotes from each warehouse to compare costs and services. Ensure you understand what’s included in the pricing.
Conduct Site Visits: Visit the warehouses to assess their facilities, operations, and overall suitability. A site visit allows you to evaluate the warehouse’s cleanliness, organization, and technology.
Reading Reviews and Checking for Industry Certifications
Read Reviews: Look for reviews and testimonials from other businesses that use the warehouse. Positive feedback and a strong reputation are good indicators of reliability.
Check for Industry Certifications: Verify if the warehouse has relevant industry certifications that demonstrate their adherence to quality and operational standards.
Asking About Customer Support and Problem Resolution
Customer Support: Inquire about the warehouse’s customer support practices. A responsive and proactive support team is essential for addressing any issues that may arise.
Problem Resolution: Ask about their approach to problem resolution. Ensure they have processes in place to handle any fulfillment challenges effectively.
Red Flags to Avoid
Be cautious of the following red flags when choosing a pick and pack warehouse:
Poor Communication or Lack of Transparency
Communication Issues: Avoid warehouses that have poor communication or are unresponsive to your inquiries. Clear and open communication is crucial for a successful partnership.
Lack of Transparency: Beware of warehouses with hidden fees or unclear cost structures. Transparency in pricing and operations is essential for a smooth working relationship.
Hidden Fees or Unclear Cost Structures
Unclear Pricing: Be wary of warehouses that do not provide a clear breakdown of their pricing. Hidden fees can lead to unexpected costs and budgeting challenges.
Lack of Flexibility in Operations or Contracts
Inflexibility: Avoid warehouses that are inflexible in their operations or contract terms. Flexibility is important to accommodate changes in your business needs.
Conclusion
Finding the right pick and pack warehouse is a crucial decision for optimizing your order fulfillment process and ensuring customer satisfaction. By understanding your business needs, evaluating key factors, and vetting potential partners thoroughly, you can find a warehouse that aligns with your goals and supports your growth.
If you need guidance on selecting the right pick and pack warehouse for your business, reach out to Slotted for expert advice and support.